Actions
[ESRS E5-2; GRI 3-3d, 306-2]
A summary of the “Actions taken” can be found in the management approach at the beginning of this chapter.
Lenzing pursues its vision by following three key practices that incorporate various elements of the circular economy into its circular business model. These practices are outlined in figure “Circular economy model” and described below:
- Natural circularity
- Resource-efficient products and technologies
- Developing commercial-scale recycling technologies
Circular economy model
Natural circularity
Origin
Lenzing’s fibers consist of cellulose, the most abundant organic polymer, which is biodegradable and mainly obtained from the renewable raw material wood. Wood at Lenzing is sourced from sustainably managed forests and plantations, which requires constant effort. For more information on certifications, please see the “Sourcing” section of the “G1 Business conduct” chapter.
LENZING™ Lyocell, Modal and Viscose Standard fibers are certified by TÜV Austria as biodegradable and compostable1. The safe disposal of these fibers in the natural environment enables the cellulose material loop to close in alignment with the biological cycle. Natural circularity covers this biological cycle and also focuses on different end-of-life solutions.
GLACIER PROTECTION FLEECE
The melting of glaciers is symbolic of the repercussions of global warming. As a company committed to science-based targets to limit the rise of global temperatures, Lenzing also seeks new product solutions that can contribute to this topic. One key example and highlight in 2023 was the development of a glacier protection fleece made 100 percent from Lenzing’s cellulose fibers. This award-winning innovation (Biodiversity and Water Award at the CNMI Sustainable Fashion Awards 2024) helps to protect glaciers without contributing to microplastic pollution.
In 2024, sheets that covered the glaciers for the summer season at six sites between Austria and Switzerland over an area of more than 20,000 square meters of snow and ice, were dismantled. After further rigorous testing, a three-step process of cleaning, drying, and tearing began, after which Lenzing will explore the next stage of this circular concept by recycling the fibers of the collected materials.
End of life
By applying a more application-specific approach, Lenzing continuously strives to look at various end-of-life solutions, such as biodegradability, recycling or reuse, depending on the material, end-products and markets. Lenzing is therefore strategically involved in policy discussions and engaged in circular initiatives to further develop and advance the world’s transition to a more holistic economy.
Resource-efficient products and technologies
Lenzing’s resource-efficient products and technologies are in place in 2024 and Lenzing strives to continuously develop those.
Biorefinery for pulp production
During pulp production, wood is turned into dissolving wood pulp for subsequent fiber production. At Lenzing’s pulp sites, this is an energy self-sufficient process that uses raw materials efficiently and has high recovery rates for solvents and chemicals. Thus, marketable biorefinery products and energy are generated and production waste is minimized (figure “Highly efficient use of the raw material wood”). The Lenzing Group operates three biorefineries in Lenzing (Austria), Paskov (Czech Republic) and Indianópolis (Brazil), offering valuable biorefinery products to other industries, thereby contributing to the maximum utilization of wood and process chemicals in a circular approach. For more detailed information on Lenzing’s product outflows, please see the “Resource outflows” section in this chapter.
Highly efficient use of the raw material wood
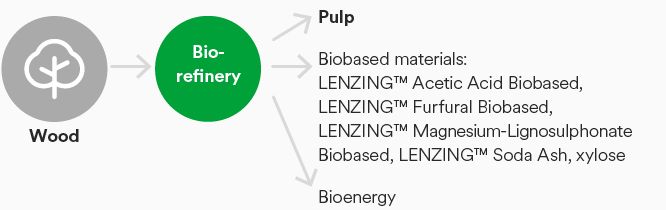
Surplus energy from pulp production is supplied as renewable energy in the form of steam and electricity. At the Lenzing (Austria) site surplus energy is directly powering fiber production lines. In Paskov (Czech Republic) and Indianópolis (Brazil) surplus energy is exported to the electricity grid and thereby supports the shift to renewable energy in these regions. This is a prime example of the cascading use of biomass and 100 percent utilization of wooden raw material.
Fiber production
Lenzing produces specialty fibers and innovates cellulose fiber technologies. The high-quality fibers, viscose (rayon), modal, and lyocell, are supplied to the textile and nonwoven industry, as well as being used in industrial applications, and are valued for their special properties.
Lenzing’s lyocell process is a closed-loop technology that allows the manufacturing of cellulose fibers using an organic solvent without chemical modification of the cellulose. The process follows a basic dissolution concept and allows 99.8 percent of the solvent to be recovered and fed back into the process. This avoids waste and ensures high resource utilization, while reducing water consumption and emissions. Production of viscose and modal fibers requires more complex chemistry but allows recovery of process chemicals that are sold to the market replacing conventionally produced substances. Generally, recovering solvents and chemicals avoids or even reduces potential environmental impacts and deploys circular economy practices. For additional information, please see the “Responsible production” focus paper.
Manufacturing steps in the textile industry
To address textile industry waste challenges, Lenzing has developed an innovative recycling technology, REFIBRA™. This technology utilizes pre- and post-consumer textile waste and turns it, together with virgin pulp, into new fibers. Lenzing’s R&D works on continuously improving the technology.
WE GIVE WASTE A NEW LIFE. EVERY DAY
In line with its vision, “We give waste a new life. Every day”, Lenzing is strives to make textile waste recycling a common standard process similar to paper recycling. Lenzing has set a target and taken measures to make this vision a reality: it plans to offer viscose, modal and lyocell staple fibers with post-consumer recycled content on a commercial scale. For more information, please see the “Sustainability targets, measures and progress” section of this chapter.
Management of production waste
There are several contexts in which waste is generated at Lenzing’s facilities, such as within production processes, as well as packaging of procured goods and sole fiber bales. Lenzing follows a waste hierarchy and avoids waste wherever possible. For more information on Lenzing`s waste, please see the “Waste management” section in this chapter.
ENABLING CIRCULARITY BY DESIGN
To advance the circular economy in the industry, Lenzing has collaborated with its long-term partner Södra in 2024 to publish their expert knowledge in a guide for designers. The guide aims to inspire designers to design their clothes in such a way that ensures the recyclability of fibers – shifting the mind set and industry towards a more circular business model. In addition, by considering different design principles in the design process, e.g. durability and longevity, reparability, fiber recyclability etc. designers can further reduce negative environmental and climate impacts in the textile industry.
To advance its circular economy practices, Lenzing uses recycled or reused materials whenever possible instead of extracting virgin resources from nature. However, it is important to note that recycling processes can require a high amount of energy due to the complex disassembly of textiles, material blends and chemicals applied in textile production. This requires a holistic approach (e.g. design for circularity; the use of renewable energy and “low-impact” chemicals in the value chain) to truly mitigate climate change and other potential environmental impacts.
For the actions taken in Lenzing’s own operations regarding the “Negative impact on the environment if waste from the textile industry is not disposed properly”, please see the “Waste management” section in this chapter.
Lenzing did not take action regarding this impact in its downstream value chain, as it has been prioritizing and working on key topics on a gradual basis.
Commercial-scale recycling technologies
Lenzing considers two types of recycling in its products: chemical and mechanical, both are in place in 2024 and continuing with no explicit end date. Pulp from chemically recycled cotton textile waste is used to produce new fibers using the REFIBRA™ technology together with virgin wood pulp. This enables a proportion of cotton waste and dissolving wood pulp to be utilized as raw materials.
LENZING™ ECOVERO™ branded viscose fibers produced with REFIBRA™ technology contain a minimum of 20 percent of recycled material from pre- and post-consumer waste. These create high-quality fibers with the same properties as fibers from virgin dissolving wood pulp. The fiber is available under the Recycled Claim Standard (RCS), certifying that all production processes in the entire supply chain have undergone the relevant steps to ensure the integrity of the final product.
Additionally, Lenzing fibers can be used as supporting blending partners for mechanically recycled textile materials (post-industrial, pre-/post-consumer). During mechanical recycling, textiles are shredded down to the individual fiber level as far as possible. Due to the shortening of fiber length and loss of performance such as tenacity, these mechanical recycled fiber materials need carrier fibers to be “respun” into new yarns. Lenzing fibers have been successfully used as carrier material for mechanically recycled fibers. For more information, please see the “Products and technologies with a net-benefit” section in the “Sustainable innovations” chapter. For actions regarding recycling, please see the ”Funding for sustainable developments“ section in the ”Sustainable innovations” chapter.
Brands/retailers
Brands and retailers not only have the influential power to provide products with recycled content to consumers, but also the ability to design textile products in a way that facilitates circularity in terms of durability, recyclability and biodegradability. Lenzing participates in an active research and development project (see CELLFIL project in the “Stakeholder engagement” section of this chapter) to further improve the utilization of pre-consumer textile waste for the production of fully biobased and biodegradable fibers.
Consumer use
Lenzing strives to offer the best possible materials for products, so that consumers and end users can purchase products according to their performance and sustainability needs.
One of Lenzing’s goals is to recycle post-consumer textile waste more efficiently. Given the complexity of global value chains, Lenzing collaborates with various stakeholders that are clearly aiming to drive systemic change in the textile and nonwoven industry.
Partnerships
In 2024, Lenzing Group has numerous ongoing long-term collaborations and partnerships to drive systemic change in the textile and nonwovens industry.
Transparency makes partnerships easier and provides a foundation for credible sustainability performance, especially regarding the circular economy as a key issue in upcoming EU legislation. Gaining a deeper understanding of Lenzing’s suppliers and downstream customers is critical to minimizing the Lenzing Group’s overall environmental as well as social impact and putting it on the right track to achieve net-zero GHG emissions by 2050 (“Long-term science-based net-zero target”).
Partnering for systemic change is one of the basic principles of Lenzing’s “Naturally Positive” sustainability strategy for jointly achieving targets with Lenzing’s stakeholders. Thus, Lenzing actively engages with suppliers to obtain chemicals with a low carbon footprint, such as sodium hydroxide produced with renewable energy. This ongoing engagement is key to reducing the carbon footprint of Lenzing’s products, and meeting scope 3 reduction targets.
Such essential collaborations are further complemented by participation in several initiatives that strive to foster the circular economy in the fashion industry. For specific details on collaborations with each stakeholder, please refer to the descriptions under each respective stakeholder in the “Stakeholder engagement” section of this chapter.
VEOCEL™ AND NAïF BABY WIPES
In 2024, LENZING™ collaborated with Naïf and introduced baby wet wipes made from VEOCEL™ branded lyocell fibers. In comparison to most other wet wipes, Naïf baby wipes are plastic-free, made from cellulose VEOCEL™ fibers using wood as a raw material, and contain only nurturing natural ingredients with no addition of alcohol or perfume. With this move, LENZING™ and Naïf aim to encourage a change in the industry from fossil-based synthetic fibers to environmentally friendly methods, while keeping sensitive baby skin at the forefront.
1 LENZING™ fibers which are TÜV certified as biodegradable (soil, fresh water & marine) and compostable (home & industrial) include the following products: LENZING™ Viscose Standard textile/nonwovens, LENZING™ Lyocell Standard textile/nonwovens, LENZING™ Modal Standard textile, LENZING™ Lyocell Filament, LENZING™ Lyocell Dry and LENZING™ Nonwoven Technology. An exception in certification exists for the LENZING™ Lyocell Filament fiber, for which the necessary tests to confirm biodegradability within a marine environment have not been conducted.